Comprehensive Guide: What is Porosity in Welding and Just How to Prevent It
Comprehensive Guide: What is Porosity in Welding and Just How to Prevent It
Blog Article
The Science Behind Porosity: A Comprehensive Guide for Welders and Fabricators
Understanding the intricate systems behind porosity in welding is vital for welders and makers making every effort for impeccable craftsmanship. From the structure of the base materials to the intricacies of the welding process itself, a wide variety of variables conspire to either worsen or relieve the visibility of porosity.
Understanding Porosity in Welding
FIRST SENTENCE:
Assessment of porosity in welding discloses crucial insights right into the honesty and high quality of the weld joint. Porosity, characterized by the presence of dental caries or spaces within the weld metal, is a typical issue in welding processes. These voids, if not properly attended to, can endanger the architectural stability and mechanical homes of the weld, resulting in potential failures in the completed product.

To identify and evaluate porosity, non-destructive screening techniques such as ultrasonic testing or X-ray inspection are usually employed. These strategies enable for the identification of inner flaws without jeopardizing the integrity of the weld. By analyzing the dimension, form, and distribution of porosity within a weld, welders can make enlightened choices to improve their welding procedures and accomplish sounder weld joints.
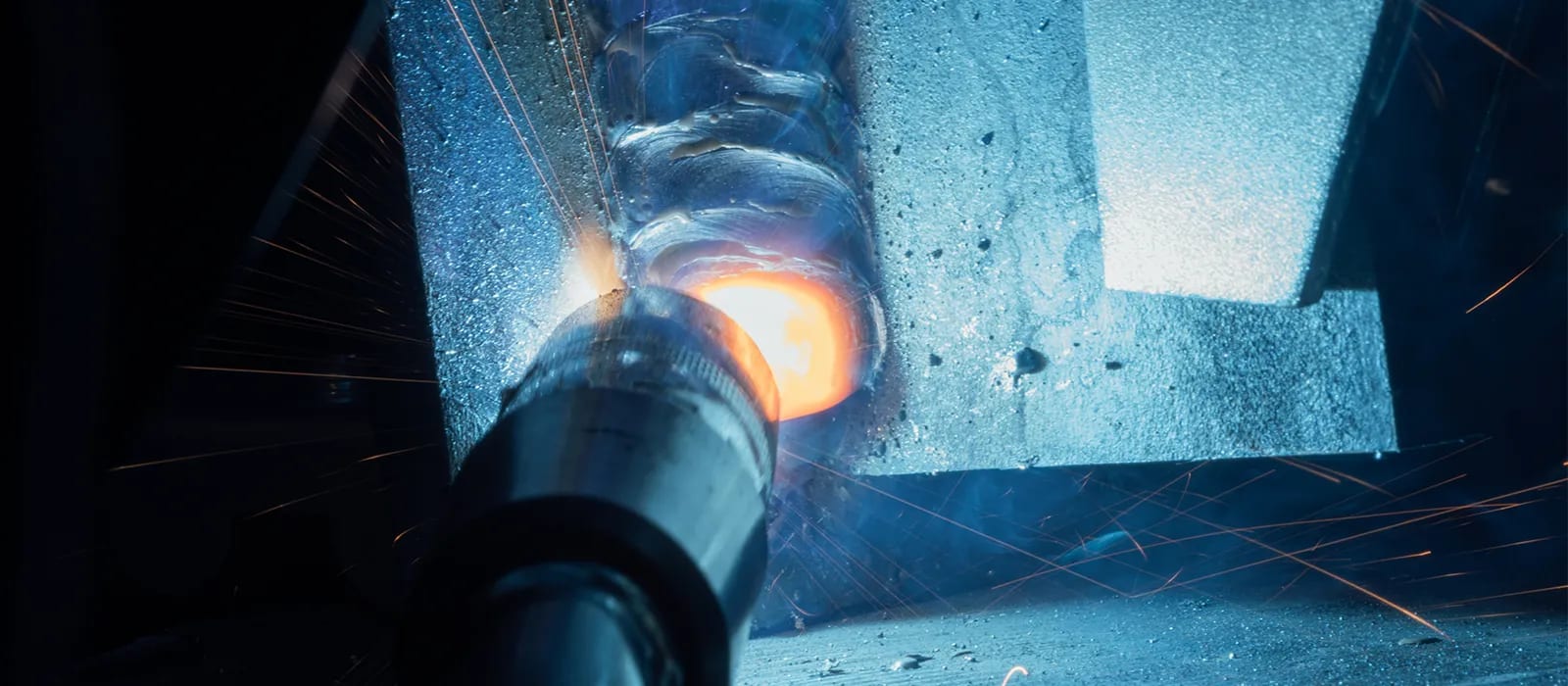
Variables Affecting Porosity Formation
The occurrence of porosity in welding is affected by a myriad of aspects, varying from gas securing effectiveness to the intricacies of welding criterion setups. One important factor adding to porosity formation is poor gas securing. When the shielding gas, commonly argon or carbon dioxide, is not effectively covering the weld pool, atmospheric gases like oxygen and nitrogen can infect the molten steel, leading to porosity. Additionally, the tidiness of the base materials plays a considerable duty. Pollutants such as rust, oil, or wetness can evaporate during welding, producing gas pockets within the weld. Welding parameters, consisting of voltage, present, travel rate, and electrode type, additionally effect porosity development. Making use of improper setups can create extreme spatter or heat input, which consequently can result in porosity. Moreover, the welding strategy utilized, such as gas steel arc welding (GMAW) or secured metal arc welding (SMAW), can affect porosity formation as a result of variations in warm circulation and gas coverage. Understanding and controlling these elements are crucial for reducing porosity in welding procedures.
Impacts of Porosity on Weld Top Quality
The visibility of porosity also weakens the weld's resistance to deterioration, as the caught air or gases within the voids can respond with the surrounding atmosphere, leading to destruction over time. Furthermore, porosity can hinder the weld's ability to withstand stress or effect, further threatening the general high quality and integrity of the welded structure. In vital applications such as aerospace, automotive, or architectural buildings, where safety and durability are paramount, the destructive effects of porosity on weld top quality can have serious consequences, highlighting the importance of lessening porosity via appropriate welding strategies and procedures.
Techniques to Lessen Porosity
Furthermore, using the ideal welding parameters, such as the correct voltage, current, and travel speed, is essential in stopping porosity. Preserving a regular arc length and angle during welding likewise assists minimize the chance of porosity.

Making use of the proper welding technique, such as back-stepping or employing a weaving motion, can webpage also aid distribute warm evenly and minimize the possibilities of porosity formation. By carrying out these techniques, welders can effectively decrease porosity and create top notch bonded joints.

Advanced Solutions for Porosity Control
Applying cutting-edge innovations and cutting-edge techniques plays a crucial role in attaining premium control over porosity in welding processes. One advanced remedy is making use of sophisticated gas combinations. Shielding gases like helium or a mix of argon and hydrogen can help decrease porosity by giving much better arc stability and boosted gas insurance coverage. Furthermore, employing sophisticated welding strategies such as pulsed MIG welding or modified environment welding can additionally aid minimize porosity problems.
An additional innovative solution includes making use of innovative welding equipment. For instance, using equipment with built-in Look At This functions like waveform control and sophisticated source of power can improve weld quality go now and minimize porosity threats. Furthermore, the implementation of automated welding systems with accurate control over specifications can significantly lessen porosity problems.
Additionally, incorporating advanced monitoring and examination modern technologies such as real-time X-ray imaging or automated ultrasonic screening can assist in discovering porosity early in the welding procedure, enabling for prompt corrective activities. On the whole, integrating these sophisticated solutions can significantly improve porosity control and boost the total high quality of bonded parts.
Verdict
In conclusion, understanding the scientific research behind porosity in welding is vital for welders and makers to produce high-grade welds - What is Porosity. Advanced services for porosity control can further boost the welding process and make sure a solid and trustworthy weld.
Report this page